

The round spout is also 3D printed (credit to Kitlaan again on Thingiverse ) I could have made the auger tube stick out the front of the box more negating the need for the spout but I wanted the top hole a littel further back from the edge so if I decide to replace the current food hopper with a larger one, the hole won't be right at the edge. The food agitator is again 3D printed and screws directly to a servo horn. You can then screw this to the wooden box and it looks nice and neat!
Automatic cat feeder manual#
I didn't want the hassle of trying to cut neat enough holes (square holes!) to mount the LCD so istead I 3D printed a home designed facia - this takes the LCD, push button (for manual feed) and the rotary encoder knob.
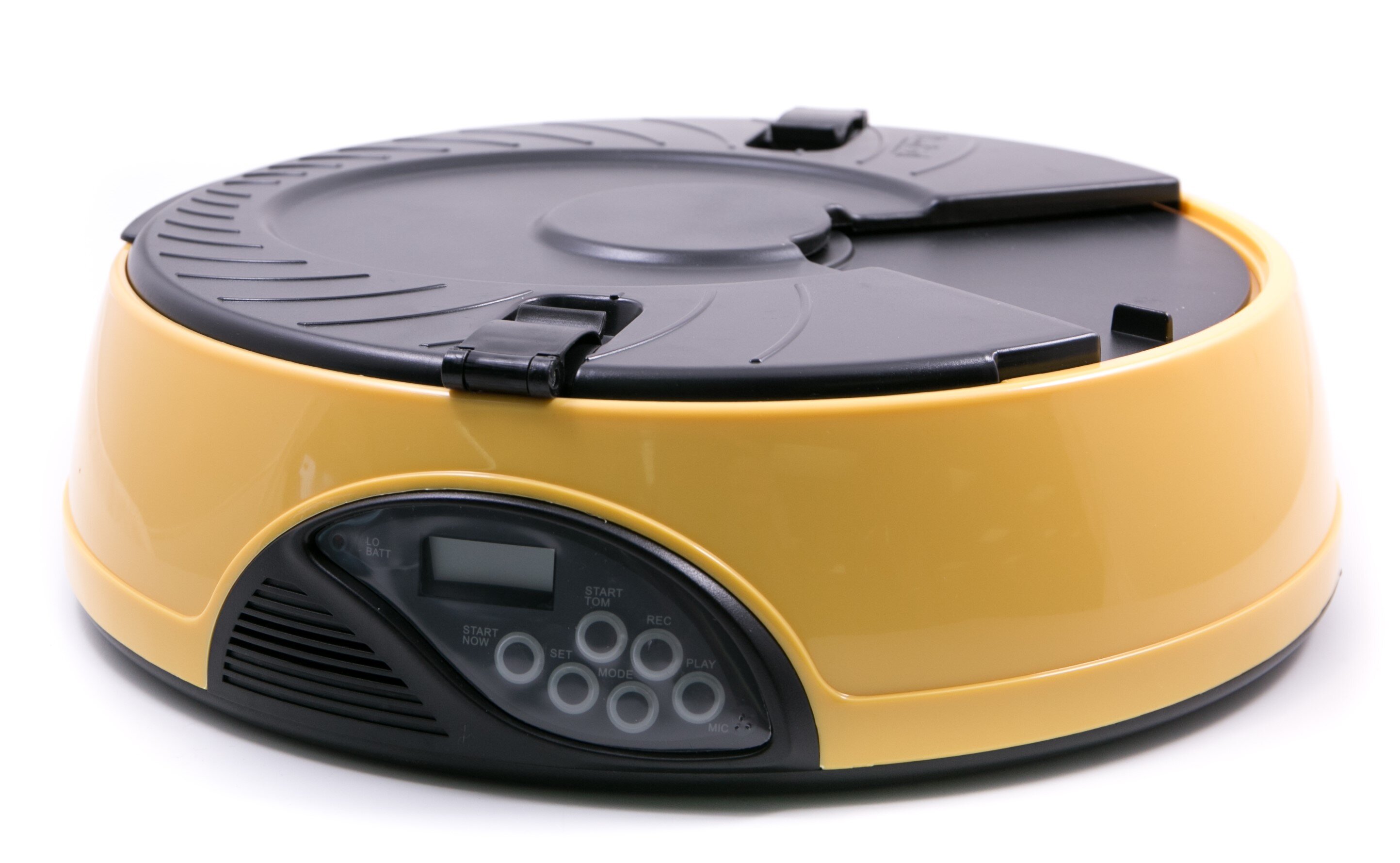
I first made a box, then cut out the base with a jigsaw, the holes for the auger with a hole cutting saw you attach to your drill, and the square holes for the control panel and servo with a jigsaw again. The box/base/enclosure is a simple MDF box (9mm). Once I was happy it would rotate without binding I fixed it in place with hot glue where it inserts into the pipe.

I screwed the servo to the auger base, making sure it was level and rotated without wobble, and then test-fitted it in a piece of 1 1/2 inch plastic T-piece tubing (commonly used for hot tub plumbing) - cost £2.90 off ebay (PVC solvent weld pipe - ponds / hot tubs etc). Just search the web - there are loads of how-to's regarding changing regular servos to continuous servos. You need it to be continuous ( no end stops) - these can be bought from places like sparkfun, but I just opened the servo, removed the plastic bump on one of the cogs that stops it rotating infinitely, and removed the potentiometer. I used a Futaba digital servo I had to hand, any servo will do, it doesn't need to be digital. You can tell slic3r to print support material for only the 1st "x" rows, but I didn't think to do that. I had to trim the base with a knife a bit where the recess for the servo horn is, as it has collapsed a fraction due to the lack of support material. I printed with no support material and it came out fine. The auger is 10cm tall, the i3 prints up to 20cm tall. I printed the auger in one go (the author provides a split version too so you can print smaller objects and glue them together) - I have a Prusa i3 which had no issues with this. The auger print comes in a few files - one for the auger, one for the servo mount/tube mount, and a servo spacer, which I didn't need. I do have experience with battery backed up real time clocks (RTC) so adding one was a no-brainer. I've previous experience with Arduino, but have never used an LCD or a rotary encoder - but it's no problem - the Arduino tutorials and examples are amazingly well written. This is where the Arduino comes in and saves the day.
Automatic cat feeder code#
His physical design is good, but the code is too simplistic for my needs, there is no display, no multiple feedings, and no user variable portion sizes. () - Credit to Kitlaan for his initial design which my machine is heavily based on. Previously this was too much of a hurdle for me, but now with 3D printing, I just downloaded a design from thingiverse and printed it! If you like tinkering, build a 3D printer! - It's fun to make and amazingly useful to own. The 1st hurdle is to make an auger (screw type feeder).
